Metrología de alta calidad para el control de calidad en la sala de medición, la producción, la entrada de mercancías o el desarrollo.
Gear Metering Pumps & Meter Mix Dispense Machines with highest accuracy for processing liquids and pastes.
High-precision rotary stroke bearings for backlash-free linear and rotational movements for use in machine and device construction.
cilíndricas Metrología de formas y de posiciones Metrología de ejes Metrología de dentados Metrología óptica Portal de máquinas usadas







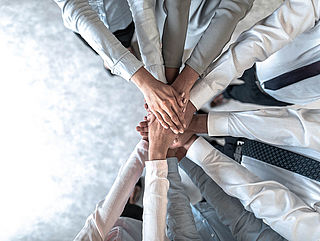
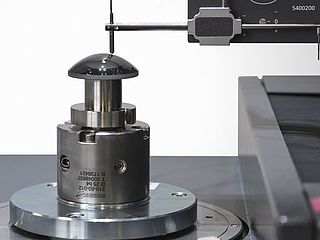
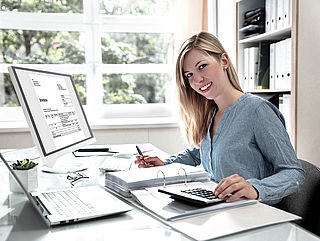










Experimente los productos más recientes de la metrología en nuestro folleto de novedades para 2021. ✓nuevas funciones ✓máxima calidad ✓innovaciones sofisticadas




Como empresa que desarrolla sus actividades en todo el mundo, Mahr no solo cuenta con patentes en Alemania, sino en muchos otros países.







Innovadora metrología manual de Mahr: Pies de rey, micrómetros y relojes comparadores en versiones analógicas y digitales con transmisión inalámbrica integrada. Los medidores comparativos y los patrones de referencia de Mahr son indispensables para una metrología de producción precisa.

Toda la gama de pies de rey comprende tanto aparatos analógicos como digitales. Manejo sencillo, sin cables y altamente preciso. Perfectos para un uso eficiente en el área de producción.

Nuestros pies de rey digitales destacan por un indicador digital de lectura fiable, así como por un diseño moderno y la precisión habitual de Mahr. El surtido abarca aparatos de medición para todas las aplicaciones. Además, las diversas interfaces para la transmisión de datos y el grado de protección hasta IP67 satisfacen todos los requisitos.

Lectura sin deslumbramientos, acero templado, guías elevadas para proteger la escala y conseguir una precisión máxima. Características de un pie de rey de calidad de Mahr con el nonio clásico.

Esfera grande y de alto contraste y mecanismo a prueba de golpes para una precisión duradera. El clásico mecánico para una lectura rápida y fiable.

Máxima precisión en las versiones más distintas. Los micrómetros de Mahr se encuentran disponibles en la variante mecánica clásica, pero también en las variantes digitales e inalámbricas.

Un indicador digital de lectura fiable, así como el diseño moderno y la precisión habitual de Mahr, son las características más destacadas de nuestros micrómetros para exteriores digitales. El surtido abarca aparatos de medición para todas las aplicaciones. Las diversas interfaces para la transmisión de datos y un alto grado de protección de hasta IP65 satisfacen todos los requisitos.

Lectura sin deslumbramientos, placas de aislamiento térmico y husillo con rectificado de precisión para una exactitud máxima. Estas son las características de un micrómetro de calidad de Mahr.

Especialmente adecuados para una comprobación segura y rápida de piezas de fabricación en serie (árboles, varillas, vástagos) La estabilidad dimensional se detecta y se lee de un vistazo en el comparador de precisión.
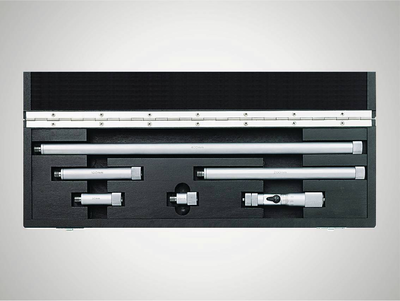
Para medir diámetros grandes y comprobar distancias de hasta 2500 mm

Con indicador analógico o digital, según se prefiera, o como medidor rápido con mango tipo pistola. Los medidores de interiores de 3 puntos de Mahr ofrecen siempre resultados de medición fiables gracias a su función de centrado automático.

Lectura sin deslumbramientos y husillo con rectificado de precisión para una máxima precisión Estas son las características de un micrómetro de calidad de Mahr.

Toda la gama de relojes comparadores, comparadores de precisión y comparadores de palanca comprende tanto aparatos analógicos como digitales. Manejo sencillo, de manera opcional, sin cables, y altamente preciso. Perfectos para un uso eficiente en el área de producción.

Un indicador digital de lectura fiable, así como la robusta construcción y la alta precisión de Mahr son las características más destacadas de nuestros relojes comparadores digitales. El surtido abarca aparatos de medición para todas las aplicaciones. Las diversas interfaces para la transmisión de datos y un alto grado de protección de hasta IP54 satisfacen todos los requisitos.

Alta sensibilidad y precisión gracias a: Robusto soporte de los ejes del mecanismo de medición, ruedas dentadas y piñones de precisión, varilla de medición de alta precisión sobre rodamiento.

Alta sensibilidad y precisión gracias a: Robusto soporte de los ejes del mecanismo de medición, ruedas dentadas y piñones de precisión, varilla de medición de alta precisión sobre rodamiento

En comparación con los relojes comparadores analógicos, los comparadores de precisión Millimess presentan componentes aún más precisos, así como una mayor precisión de medición y una histéresis optimizada. Estas ventajas se reflejan sobre todo en las comprobaciones de salto radial, así como en las mediciones de rectitud y planitud y en las mediciones comparativas.

Los comparadores de precisión inductivos Millimess son altamente precisos y permiten obtener resoluciones de hasta 0,2 μm. Las funciones de manejo orientadas a la práctica, como la vigilancia de tolerancias, el registro de los valores mínimo y máximo en mediciones dinámicas, un indicador analógico y digital combinado y una transferencia de datos sencilla, los convierten en medidores de precisión indispensables.

El mecanismo de medición, sensible y optimizado por ordenador, garantiza un nivel máximo de seguridad y precisión. Y, para el uso en el arduo entorno del taller, la pantalla está protegida contra arañazos o roturas gracias a una magnífica lámina de cristal mineral templado impermeabilizada, mientras que una junta impide de forma fiable la penetración de líquidos.

Un indicador digital de fácil lectura, así como la robusta construcción y la alta precisión de Mahr, son las características más destacadas de nuestros comparadores de palanca digitales.

Los palpadores de medición 3D de Mahr para máquinas NC, centros de mecanizado y máquinas de erosión reducen los tiempos de preparación y de inactividad, lo que resulta perfecto para el palpado preciso de bordes de referencia en piezas de trabajo y dispositivos.

Integrated Wireless, módulos inalámbricos externos, USB, Opto RS232 o Digimatic: Independientemente del estándar de interfaz que utilice, MarConnect garantiza siempre una conexión óptima.

Muchos medidores manuales de Mahr disponen de una salida de datos con interfaz MarConnect Independientemente del estándar de interfaz que utilice (USB, Opto RS-232 o Digimatic), MarConnect garantiza siempre una conexión óptima.

La gama inalámbrica de Mahr garantiza resultados de medición exactos con una absoluta libertad de movimiento, pues puede medir de forma moderna y sencilla, sin tener que depender de las tecnologías que utilizan cables.

Gracias a su estable estructura, los soportes de medición, las mesas de trabajo y los bancos de centrar MarStand forman la base imprescindible para obtener resultados de medición exactos. Los relojes comparadores, los comparadores de precisión, los comparadores de palanca y los palpadores de medición obtienen aquí el apoyo que necesitan.
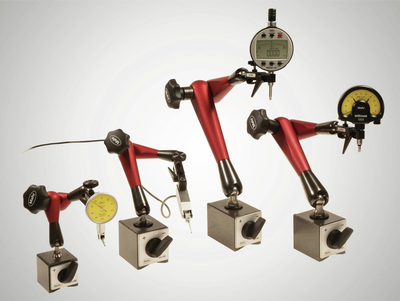
Gracias a su estable estructura, los soportes de medición forman la base imprescindible para obtener resultados de medición exactos. Los relojes comparadores, los comparadores de precisión, los comparadores de palanca y los palpadores de medición obtienen aquí el apoyo que necesitan.
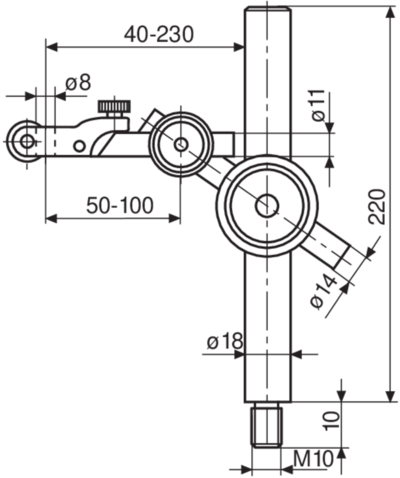
Gracias a su estable estructura, los varillajes de medición MarStand se utilizan en soluciones individuales y forman la base imprescindible para obtener resultados de medición exactos. Los relojes comparadores, los comparadores de precisión, los comparadores de palanca y los palpadores de medición obtienen aquí el apoyo que necesitan.

La combinación de una mesa de trabajo precisa y plana, una columna de medición estable y unos robustos componentes del brazo son las características de las mesas de trabajo. Gracias a su estructura extremadamente estable, las mesas de trabajo MarStand constituyen la base imprescindible para obtener resultados de medición exactos.

Los bancos de centrar son el método más sencillo para determinar errores de posición y de forma en árboles en los entornos cercanos al área de producción. Gracias a la versatilidad de los modelos, los robustos bancos de centrar MarStand constituyen la base para cumplir los requisitos más diversos de las piezas de trabajo, así como para obtener resultados de medición exactos.
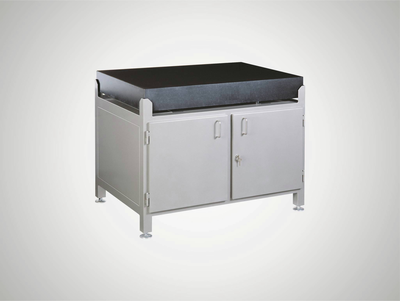
Gracias a su magnífica resistencia y a su enorme estabilidad, las placas de comprobación de granito constituyen la base perfecta para sus medidores de altura.

En su calidad de medidores comparativos, los aparatos de medición indicadores representan la herramienta perfecta para mediciones de precisión en el área de producción. El ajuste respecto a un patrón de referencia disminuye el margen de desviación y reduce al mínimo el efecto que pueden tener las oscilaciones de temperatura en los resultados de medición.

Los calibres de herradura con comparador de precisión son los aparatos de medición perfectos para mediciones de precisión de piezas cilíndricas como árboles, pernos y vástagos, sobre todo para comprobaciones fiables y rápidas en piezas de fabricación en serie. La estabilidad dimensional se detecta y se lee de un vistazo y de forma fiable en el comparador de precisión.

Los medidores de interiores representan las herramientas perfectas para mediciones de precisión en taladros de diámetros, así como para mediciones exactas de redondez y conicidad.

Con nuestros medidores de espesores, ofrecemos una gama robusta y sencilla para una medición tremendamente sencilla de láminas, chapas y placas de cualquier tipo.

Cuando no es posible utilizar aparatos de medición estándar, como los pies de rey o los micrómetros de interiores debido a la geometría de la pieza de trabajo, los aparatos de medición con brazo de palpado son la solución perfecta.
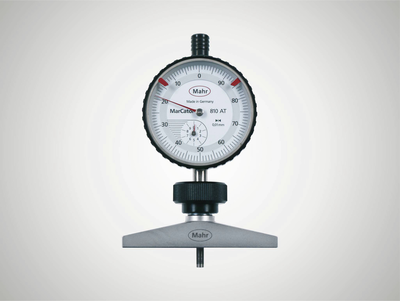
Con nuestros puentes de medición de profundidad, ofrecemos una gama robusta y sencilla para realizar mediciones de profundidad especialmente rápidas. Gracias al vástago de sujeción de 8 mm, es posible utilizar relojes comparadores, comparadores de precisión y palpadores, en función de la tarea de medición de que se trate.

En su calidad de aparatos de medición comparativos, los medidores universales son el perfecto aliado para mediciones de precisión en el área de producción, pues la medición comparativa respecto a un patrón de referencia reduce al mínimo el efecto que pueden tener las oscilaciones de temperatura en los resultados de medición.

Independientemente de si se trata de dentados, roscas, conos o muescas, los medidores universales Multimar ofrecen una solución óptima para casi todas las mediciones interiores y exteriores en las que no es posible utilizar medidores estándar. De este modo, el usuario dispone de diferentes aparatos básicos y de una amplia oferta de accesorios.

Ajuste sus medidores de interiores y exteriores de forma precisa. Con los aparatos de ajuste 844 S estará equipado de forma óptima para cualquier tarea de medición, incluso en el caso de grandes dimensiones.

Independientemente de si se trata de ruedas de centrado, piezas estrechas o muescas, los medidores universales Multimar 36B ofrecen una solución óptima para prácticamente todas las mediciones interiores y exteriores. De este modo, el usuario dispone de diferentes aparatos básicos y de una amplia oferta de accesorios.

Confíe en los patrones y los calibres de Mahr, pues constituyen la base para obtener resultados de medición exactos.

Confíe en los patrones de ajuste de Mahr, pues constituyen la base para obtener resultados de medición exactos.

Los bloques patrón de Mahr le ofrecen patrones de referencia y de trabajo de alta calidad. Puede elegir entre 4 clases de tolerancia y 2 materiales en función de las necesidades de su taller, su producción o sus requisitos de control de calidad.

Las varillas calibradas de Mahr se encuentran disponibles en 3 clases de tolerancia y diferentes modelos. Elija la opción adecuada en función de las necesidades de su taller, sus condiciones de producción o sus requisitos de control de calidad.

Las exigencias que se les imponen a los medidores de longitudes eléctricos son tan amplias como el abanico de sus aplicaciones. Estas aplicaciones requieren altos niveles de fiabilidad y precisión, combinados con un manejo sencillo.
Las exigencias que se les imponen a los medidores de longitudes eléctricos son tan amplias como el abanico de sus aplicaciones. Estas aplicaciones requieren altos niveles de fiabilidad y precisión, combinados con un manejo sencillo. Los medidores de columnas y compactos Millimar cumplen estos requisitos.
Los medidores de longitudes Millimar son compactos, robustos y fáciles de manejar. Son aparatos indicadores y de evaluación de uso universal para tareas de medición de complejidad manejable en el área de producción y en las salas de medición.

Las numerosas posibilidades de combinación de módulos y software permiten configurar el entorno de trabajo y las herramientas de forma más individualizada que nunca.
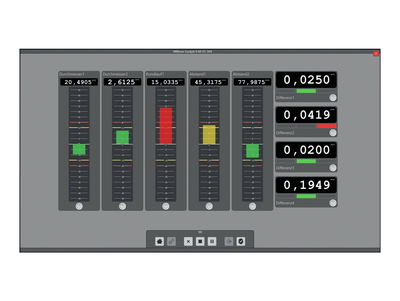
Software inteligente y de uso universal para tareas de medición complejas en el área de producción

Los instrumentos de medición Millimar son el componente más decisivo de la cadena de medición. De hecho, sus características determinan la calidad de toda la medición. Por ello, dependiendo del tipo de aplicación de que se trate, le ofrecemos diferentes tecnologías. Tal es el caso de los palpadores de medición inductivos Millimar: robustos, con una amplia variedad de aplicaciones y a un precio muy atractivo.

No importa si está realizando mediciones de espesores, de saltos radiales o de concentricidad: los palpadores inductivos permiten registrar valores de medición y desviaciones independientemente de la forma, del apoyo o de las desviaciones de salto radial. Su gran ventaja es el amplio margen de linealidad y la relativa insensibilidad frente a las influencias externas. Los palpadores se utilizan predominantemente para mediciones comparativas en el área de producción, por lo que las funciones específicas del sensor pueden variar de un caso a otro.
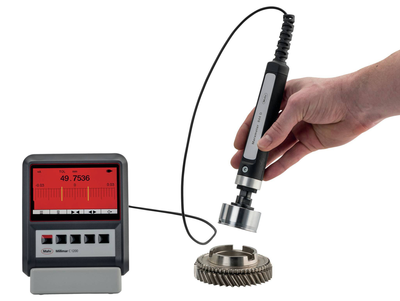
Los tampones lisos son especialmente adecuados para la comprobación rápida del diámetro, la redondez y la conicidad en taladros. Como no es preciso buscar un punto de inversión, como sucede con otros medidores de interiores, resultan especialmente adecuados para el uso en combinación con aparatos indicadores digitales y para el procesamiento posterior de los valores de medición.

Los medidores de longitudes neumáticos destacan por su alta precisión y su gran estabilidad durante toda su vida útil. Además, gracias a la medición sin contacto con boquillas de medición, no se producen daños en las piezas de trabajo. También es posible medir de forma segura y sin problemas piezas de trabajo sin limpiar, aceitadas, engrasadas o cubiertas de pasta de lapeado, pues el aire de medición limpia los puntos de medición.
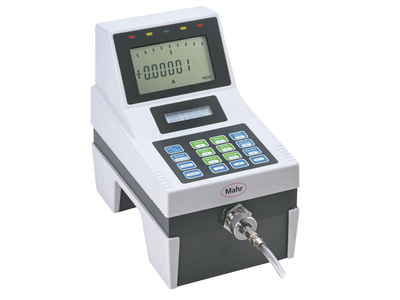
Los medidores de longitudes Millimar son compactos, robustos y fáciles de manejar. Son aparatos de visualización y evaluación de uso universal para tareas de medición de complejidad manejable en el área de producción.

Los resultados de medición se presentan en 101 diodos luminosos de tres colores, lo que permite leerlos de forma extremadamente sencilla incluso a distancia. Si se superan los límites de advertencia y de tolerancia programables, los segmentos correspondientes cambian de color y pasan de verde a amarillo o a rojo.

Los medidores neumáticos Millimar registran desviaciones dimensionales de forma rápida y precisa. Llevan años demostrando su eficacia como medidores de longitudes neumáticos de alta calidad, tanto en el ámbito de la producción industrial como en las salas de medición.

Cuando las tareas de medición y evaluación deben realizarse de forma móvil.
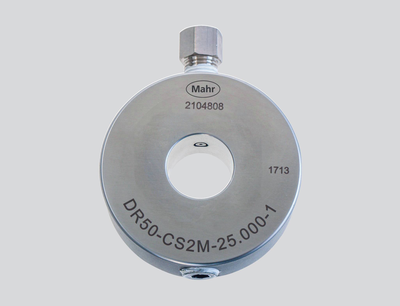
Medición sin contacto con anillos de medición neumáticos sin dañar las piezas de trabajo.

Adapte la estación de medición a sus tareas de medición gracias a los accesorios disponibles para la metrología neumática.

Confíe en los patrones de ajuste de Mahr, pues constituyen la base para obtener resultados de medición exactos

Ajuste de aparatos de medición neumáticos (anillos de medición con tobera). Templados, envejecidos, rectificados y lapeados con sumo cuidado.

Ajuste de aparatos de medición neumáticos (tampones neumáticos). Templados, envejecidos, rectificados y lapeados con sumo cuidado.

Los niveles de burbuja electrónicos ofrecen una reacción rápida, una resolución precisa y una magnífica reproducibilidad.
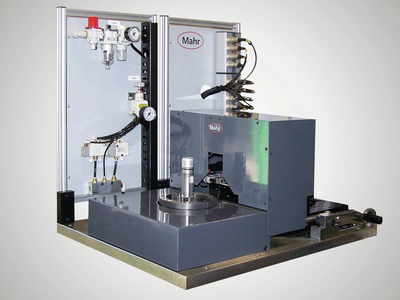
Cuando lo estándar ya no es suficiente: Soluciones individuales adaptadas a los deseos del cliente

¿Desea alcanzar la máxima precisión con sus mediciones? Si es así, confíe en Digimar.

Para el trazado y el marcado de piezas de trabajo en el taller. Medición sencilla de alturas y distancias.
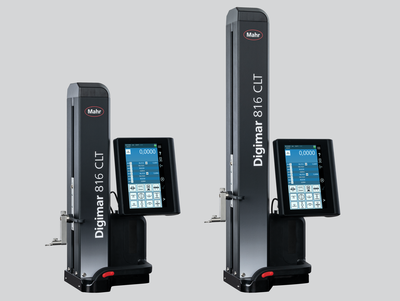
Touch operation, ergonomic handling and a wide range of evaluation options: This is what the Digimar 816 CLT height measuring device stands for.
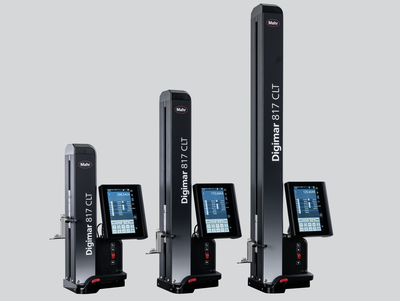
Manejo mediante pantalla táctil, manipulación ergonómica y numerosas posibilidades de evaluación. Estas son las características del medidor de altura Digimar 817 CLT.

La metrología de longitudes de precisión representa una metrología dimensional de máxima precisión, tanto en mediciones absolutas como en relativas.
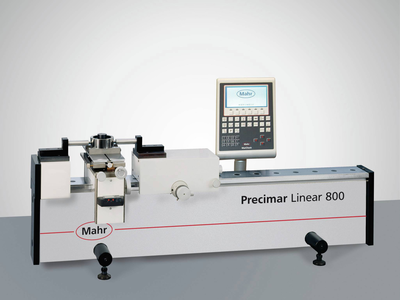
Aparatos de medición de longitudes y de ajuste universales y fáciles de manejar para el área de producción
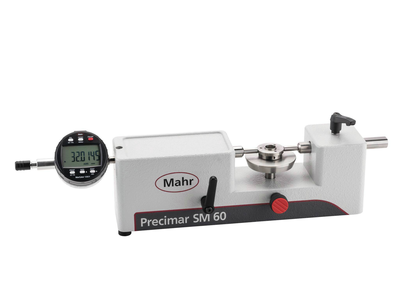
Aparatos de medición de longitudes y de ajuste universales y fáciles de manejar para el área de producción

Gracias a la amplia gama de productos que comprenden desde aparatos básicos como el banco de ensayo de bloques patrón, el banco de relojes comparadores totalmente automático y los aparatos ULM, hasta la máquina de medición universal CiM ultra precisa y parcialmente automática, Mahr ofrece siempre una solución práctica óptima, tanto para el área de producción como para las salas de medición y los laboratorios de calibración. Dicho de otro modo: Metrología de la máxima precisión en procesos de medición extremadamente eficaces.

No importa si se trata de aparatos clásicos ULM o motorizados PLM y CiM. Las máquinas de medición de longitudes universales de Mahr permiten una medición sencilla, rápida y fiable con una incertidumbre mínima.

Comprobación parcial y totalmente automática de relojes comparadores, comparadores de palanca, comparadores de precisión y palpadores, de forma eficiente y precisa.

Comprobación parcial y totalmente automática de relojes comparadores, comparadores de palanca, comparadores de precisión y palpadores, de forma eficiente y precisa.

Comprobación manual de relojes comparadores, comparadores de palanca y comparadores de precisión, de forma sencilla y precisa

Confíe en los bancos de ensayos de bloques patrón de Mahr, pues constituyen la base para la comprobación precisa de sus patrones

Casi todas las industrias utilizan microscopios para la comprobación rápida de distancias, radios y ángulos. Tanto en el laboratorio como cerca del área de producción.

Microscopios estéreo con zoom con óptica de alta calidad para imágenes tridimensionales nítidas y brillantes. Binoculares o trinoculares con uso adicional de cámaras digitales.

Casi todas las industrias utilizan microscopios para la comprobación rápida de distancias, radios y ángulos. Tanto en el laboratorio como cerca del área de producción.

Metrología de superficies para la industria y la investigación

Las superficies funcionales estructuradas con tolerancias estrechas exigen sistemas de medición altamente precisos que sean capaces de registrar en poco tiempo toda la topografía de una pieza de trabajo o de un objeto.

La metrología de contornos sirve para determinar desviaciones globales de forma.


Mida contornos precisos con aparatos de medición ópticos

Medición combinada de contornos y rugosidad: Profesional para todos los casos
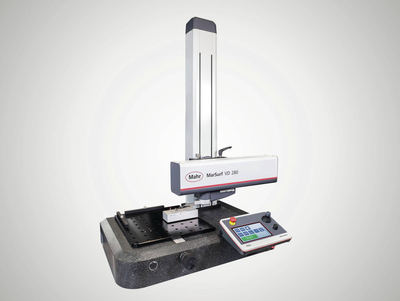
Medición combinada de contornos y rugosidad: Profesional para todos los casos

Medición de contornos y de rugosidad 2D/3D según la norma ISO 25178/ISO 4287

Metrología de superficies 3D para la industria y la investigación

Mida en todas partes con aparatos de medición móviles.
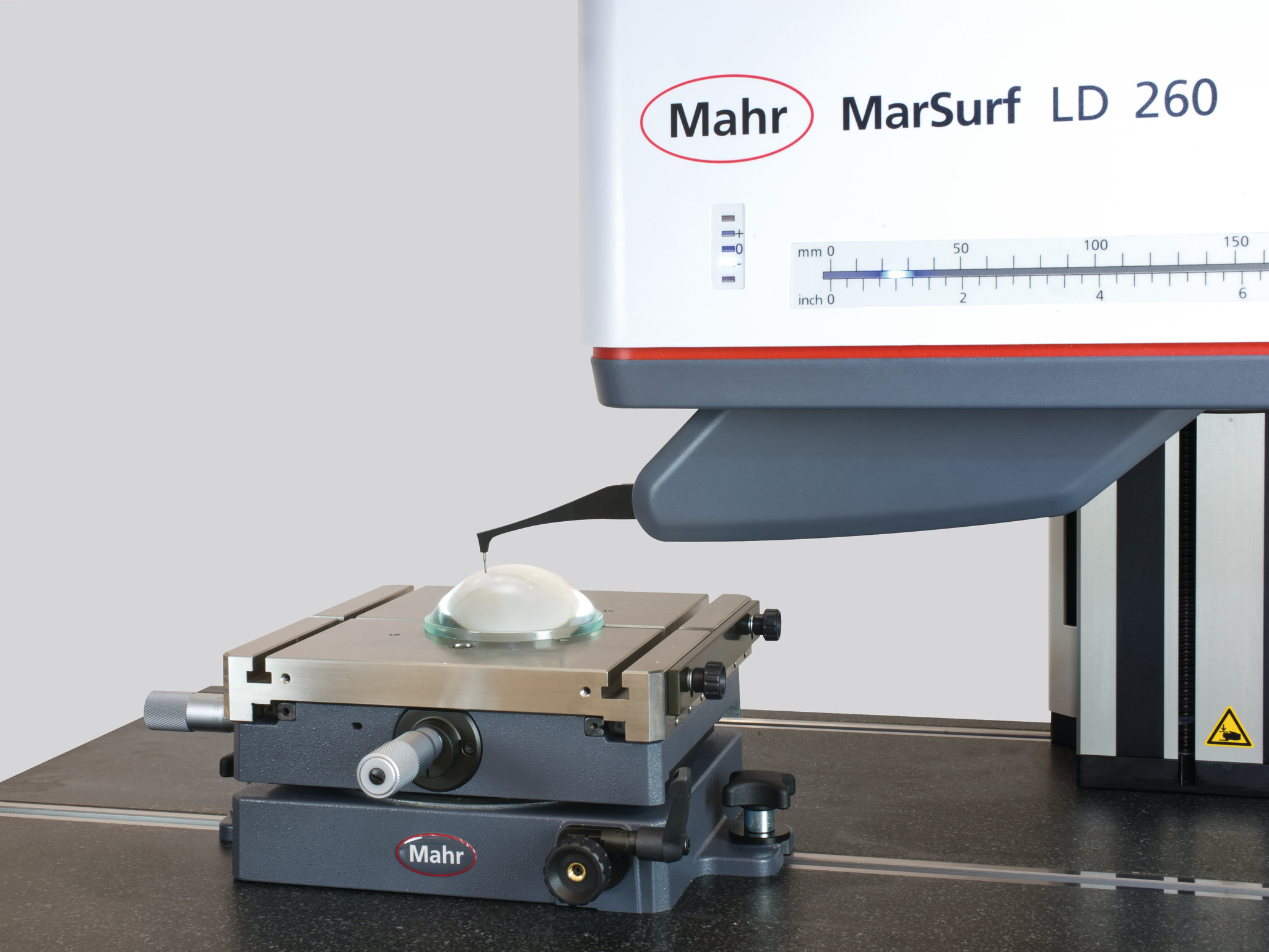
Estaciones de medición para la medición de elementos ópticos altamente precisos

Cuando lo estándar ya no es suficiente: Soluciones individuales adaptadas a los deseos del cliente

Las superficies funcionales estructuradas con tolerancias estrechas exigen sistemas de medición altamente precisos que sean capaces de registrar en poco tiempo toda la topografía de una pieza de trabajo o de un objeto.
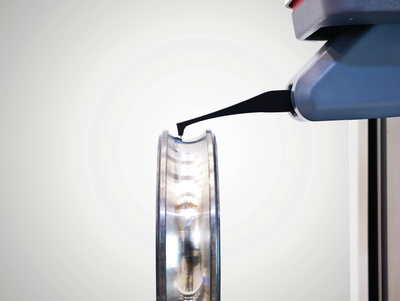
Versátiles y potentes tanto en la sala de medición como en el laboratorio.
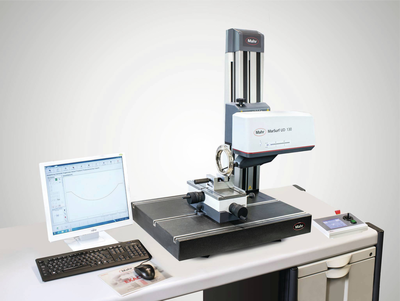


Medición combinada de contornos y rugosidad: Profesional para todos los casos
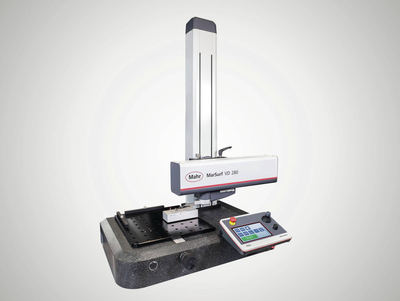
Estaciones de medición táctiles para mediciones de contornos y rugosidad

Medición de contornos y de rugosidad 2D/3D según la norma ISO 25178/ISO 4287

Metrología de superficies 3D para la industria y la investigación

Mida en todas partes con aparatos de medición móviles.
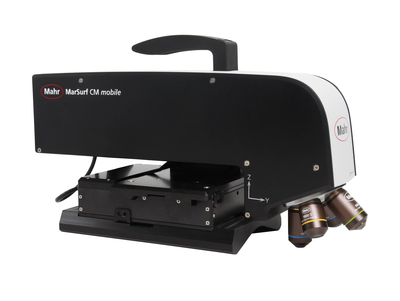
Metrología móvil de superficies 3D para
el uso in situ

Con los medidores portátiles podrá medir de forma precisa allí donde necesite los resultados.
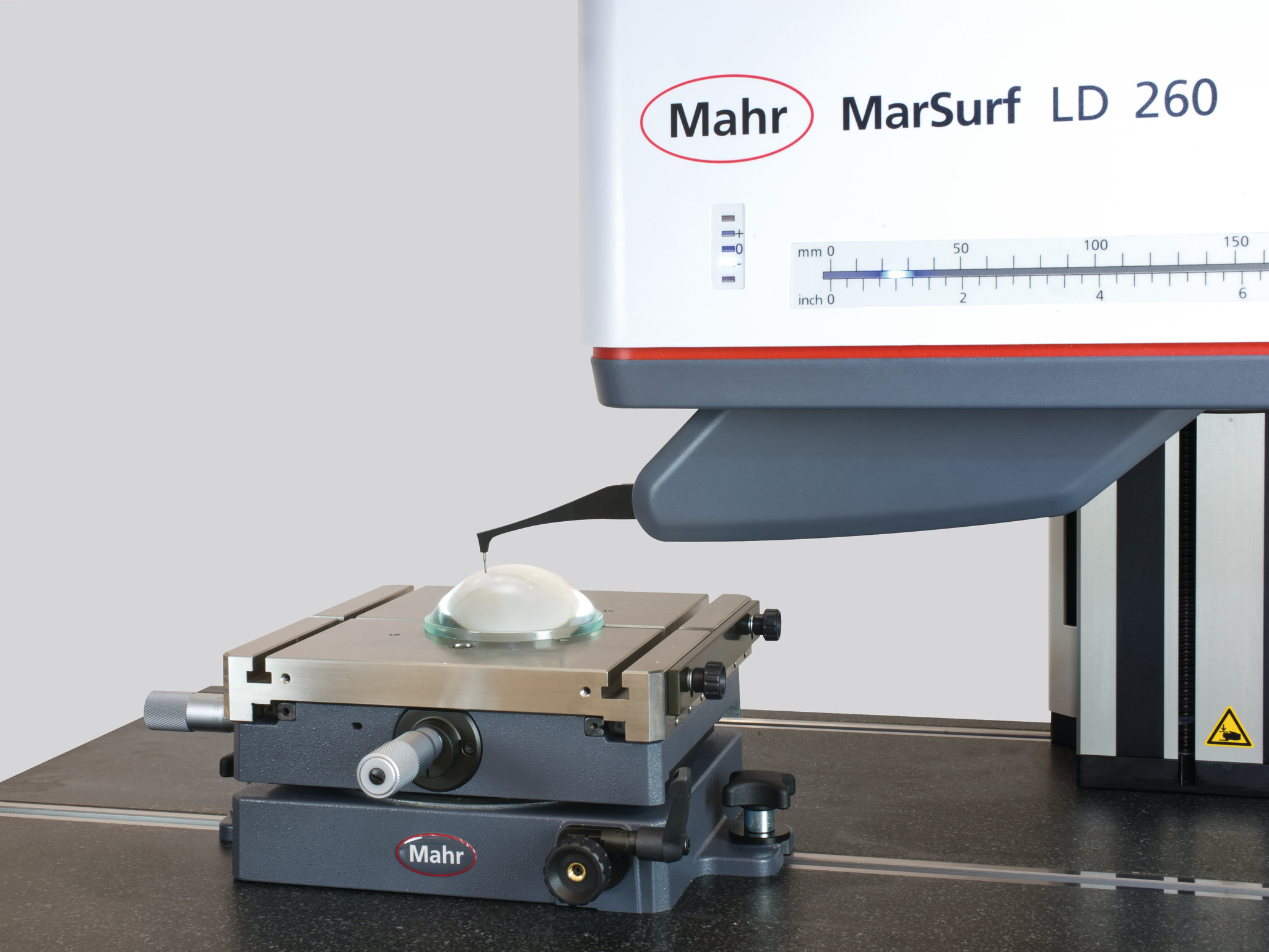
Estaciones de medición para la medición de elementos ópticos extremadamente sensibles

Cuando lo estándar ya no es suficiente: Soluciones individuales adaptadas a los deseos del cliente
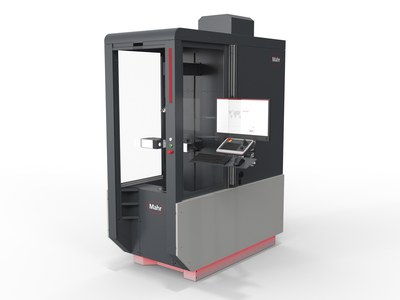
cilíndricas
Experimente características de equipamiento sobresalientes combinadas con una flexibilidad extrema en cuanto al tamaño de la pieza de trabajo y aumente su productividad en el área de producción.
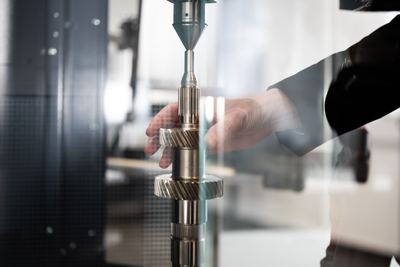
Flexible measurement of workpieces that can be clamped between centers
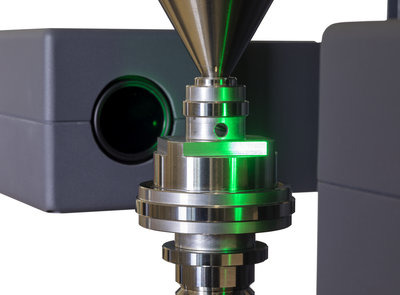
Cámara matricial de alta resolución y muy rápida para medir un gran número de características en piezas de trabajo con simetría de rotación.

Rápida cámara de matriz óptica en combinación con sistemas de palpado de alta precisión para medir una gran cantidad de características de piezas de trabajo con rotación simétrica.
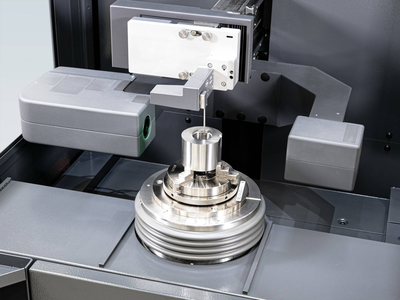
Flexible clamping options and high-precision alignment using a fully automatic centering and tilting table
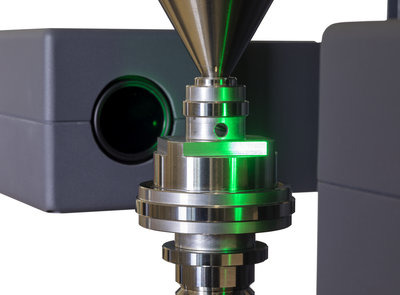
Cámara de matriz óptica de alta resolución y muy rápida para medir una amplia gama de piezas de trabajo con simetría de rotación. Incorporación de una mesa de centrado e inclinación totalmente automática para una alineación mecánica extremadamente rápida y opciones de sujeción flexibles.

Rápida cámara de matriz óptica en combinación con sistemas de palpado de alta precisión para medir una gran cantidad de características de piezas de trabajo con rotación simétrica. Complemento de una mesa de centrado y basculado para realizar orientaciones mecánicas de forma extremadamente rápida, con opciones de sujeción flexible y apto incluso para mediciones interiores.

Sistemas para la medición de tolerancias de forma y de posición, como la redondez, la planitud, la rectitud o la coaxialidad. Desde el aparato manual al totalmente automático.
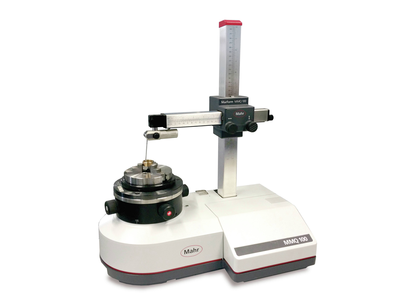
Mida características como la redondez, la rectitud o el salto radial de forma sencilla y asequible y, al mismo tiempo, altamente precisa. Nuestras medidoras de formas manuales son aptas tanto para salas de medición como para mediciones cerca del área de producción.
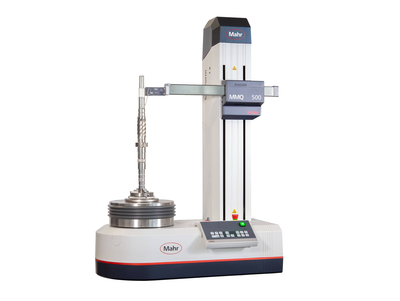
Nuestros sistemas de medición de formas automáticos le ayudan a reducir los costes de procesos, pero sin aumentar los costes de verificación: gracias a aparatos estables e innovadores que ofrecen un máximo nivel de automatización, flexibilidad y precisión.
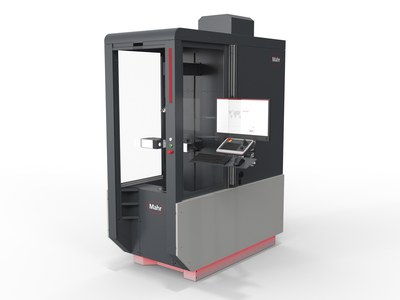
cilíndricas
Experimente características de equipamiento sobresalientes combinadas con una flexibilidad extrema en cuanto al tamaño de la pieza de trabajo y aumente su productividad en el área de producción.
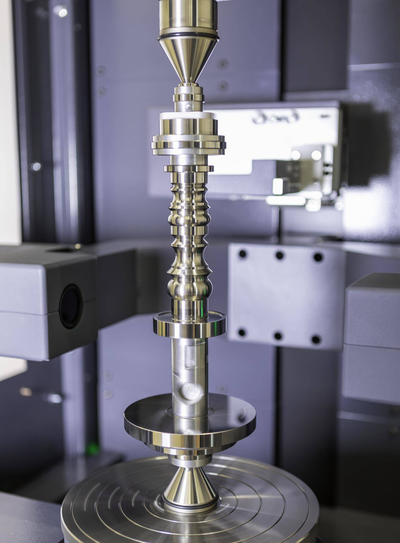
Flexible measurement of workpieces that can be clamped between centers
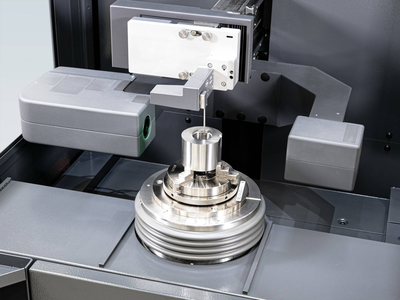
Flexible clamping options and high-precision alignment using a fully automatic centering and tilting table

Medidores ópticos y táctiles de ejes para el uso en el arduo entorno de producción. Medición completa de todas las piezas de trabajo habituales con rotación simétrica.
.
Robustos medidores ópticos de árboles universales y totalmente automáticos diseñados para su uso en el arduo entorno del taller.
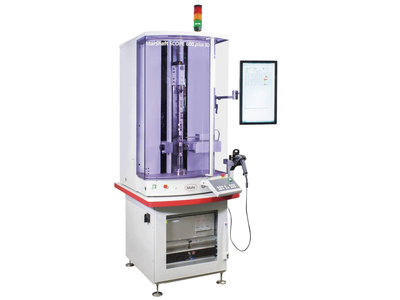
Medidores óptico-táctiles de árboles para el uso en el arduo entorno de producción. Medición completa de todas las piezas de trabajo convencionales con rotación simétrica
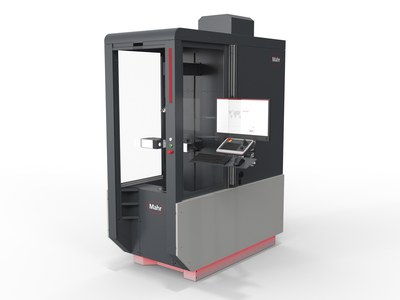
cilíndricas
Experimente características de equipamiento sobresalientes combinadas con una flexibilidad extrema en cuanto al tamaño de la pieza de trabajo y aumente su productividad en el área de producción.
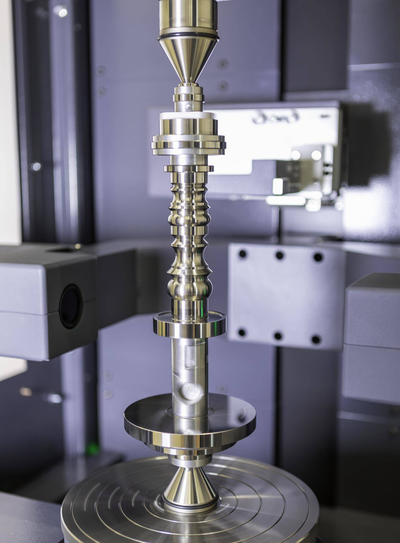
Flexible measurement of workpieces that can be clamped between centers
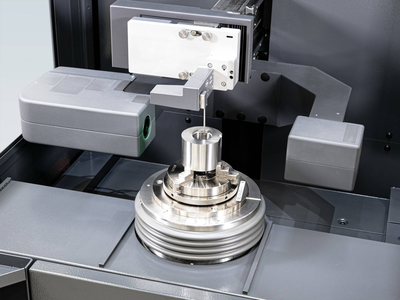
Flexible clamping options and high-precision alignment using a fully automatic centering and tilting table
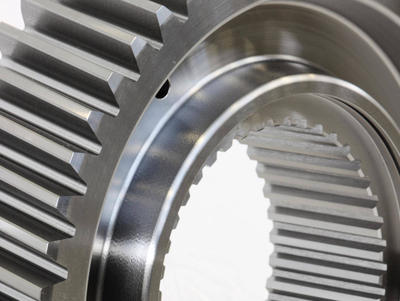
Desde los análisis de centrados altamente especializados hasta la medición en serie totalmente integrada. Mahr es su aliado en todos los niveles de las modernas ruedas dentadas y transmisiones de hoy en día.
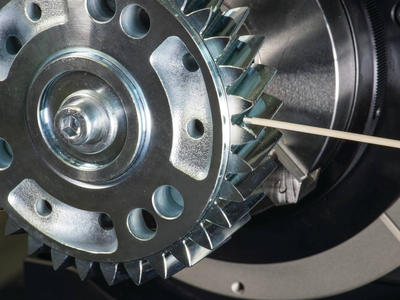
Mida exactamente en el punto en el que surja su producto, con una confirmación rápida del proceso de producción para evitar rechazos de piezas.


Amplio espectro de tecnologías y productos para un registro rápido y sin contacto de superficies y geometrías.

Casi todas las industrias utilizan microscopios para la comprobación rápida de distancias, radios y ángulos. Tanto en el laboratorio como cerca del área de producción.

Determinación de la rugosidad, del contorno y de muchos otros parámetros de superficie.

Metrología de superficies para la industria y la investigación

Rugosidades mínimas con una precisión de nanómetros

Análisis visual de topografías de superficies y geometrías

Sistemas reacondicionados con la calidad acreditada de Mahr
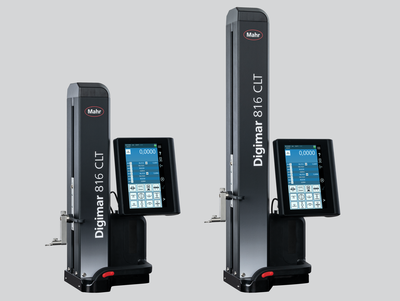
Touch operation, ergonomic handling and a wide range of evaluation options: This is what the Digimar 816 CLT height measuring device stands for.
Medición de formas: comprensión de los problemas más frecuentes
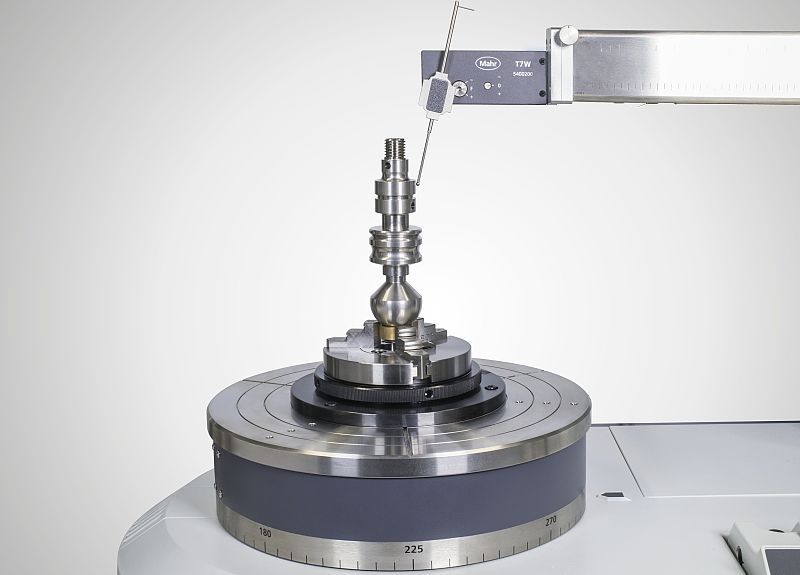
En el caso más sencillo, la medición de formas incluye un palpador de medición y un brazo de palpado con un elemento de palpado que se mueve a lo largo de una trayectoria circular o lineal ideal para registrar datos sobre los movimientos del palpador en relación con esta geometría ideal. El análisis suele ser tremendamente sencillo. Los puntos de datos medidos se filtran y es posible realizar operaciones matemáticas con ellos para determinar los resultados. Aunque se trata de una de las mediciones más básicas para apoyar muchos procesos de fabricación, algunos pasos se realizan a menudo de forma incorrecta. Los errores más frecuentes se producen a la hora seleccionar el filtro y el elemento de palpado.
Uso de filtros incorrectos
Históricamente, para las mediciones de redondez, se utilizaban 50 UPR como valor predeterminado. Aunque este filtro puede ser adecuado para numerosas aplicaciones, no lo es para todas. La nueva norma DIN EN ISO 1101:2017-09 permite especificar en el plano un ajuste de filtro adecuado directamente con cada tolerancia de forma. No obstante, la correcta elección del filtro debe seguir dependiendo de la tarea de medición. Los departamentos de diseño, planificación del trabajo y gestión de calidad tienen la responsabilidad de definir los ajustes de los filtros relacionados con los requisitos, así como de registrarlos en las normas internas y prescribirlos para todos los proveedores internos y externos.

En la práctica real, la medición de formas es un proceso para medir las desviaciones de forma. Tradicionalmente, esta labor se ha llevado en laboratorios climatizados y ha corrido a cargo de especialistas altamente cualificados, pero hoy en día suele realizarse directamente en el taller y corre a cargo empleados a los que se les confían tareas muy diversas. Independientemente de si se utiliza la medición de la forma o de la rugosidad, el procedimiento es básicamente el mismo. En cualquier medición de superficies, se suelen utilizar numerosos puntos de palpado para representar toda la superficie. Estos puntos se filtran a continuación para obtener solo los datos deseados. Por ejemplo, cuando se comprueba la rugosidad de una superficie, los datos de longitud de onda más corta se conservan para el análisis, mientras que los datos relacionados con la forma se descartan, pues esta información no es necesaria. En cambio, en la medición de formas, se filtran y eliminan los datos de longitud de onda corta para poder medir los datos de longitud de onda larga, que son los que representan la forma. Este es el primer punto en el que muchos usuarios cometen errores. Los sutiles matices del filtrado no siempre son fáciles de entender y, por lo tanto, a menudo se eligen los filtros equivocados.
De hecho, los filtros de medición de formas resultan confusos para muchos metrólogos. Por ejemplo, cuando se habla de la medición de la rugosidad de superficies, se hace referencia a los ajustes del filtro en términos de milímetros o pulgadas. Si el filtro se establece en 0,8 mm, significa por lo general que las desviaciones de superficie de menos de 0,8 mm se consideran una rugosidad superficial, mientras que los elementos de más de 0,8 mm se consideran defectos de forma de la superficie.
Sin embargo, los filtros de forma para las mediciones de redondez suelen especificarse como tamaño angular, en lugar de como longitud o distancia. Además, para que todo resulte aún más confuso, los datos de las especificaciones no se expresan directamente en grados de ángulo, sino en lo que se denomina «ondulaciones por revolución» (UPR, por sus siglas en inglés.). Así, muchos usuarios eligen 50 UPR como valor predeterminado estándar, lo que significa que la longitud del filtro equivale a una 50ª parte de un círculo, es decir, a 7,2 grados.
Tener en cuenta el diámetro de la pieza de trabajo a la hora de seleccionar el filtro
Se da la circunstancia de que la longitud del arco, que corresponde a 7,2 grados en la superficie de un objeto redondo, cambia con el diámetro (d) del objeto. Una fórmula sencilla para la circunferencia de un cilindro es: π × d, es decir, un cilindro de 4 mm de diámetro tendría una circunferencia de 12,57 mm y, por lo tanto, 7,2 grados cortarían una longitud del arco que mida 0,25 mm a lo largo de la superficie. En cambio, si es preciso medir un cilindro de 20 mm de diámetro, este tendría una circunferencia de 62,83 mm y los 7,2 grados corresponderían a una longitud del arco de 1,26 mm. Así, si se mantiene el mismo ajuste de filtro de 50 UPR en el aparato de medición, en el caso de la pieza de mayor tamaño, se tienen en cuenta desviaciones de superficie cinco veces mayores que el límite entre las características de forma y rugosidad de la superficie. En prácticamente todos los aparatos de medición, la configuración del filtro puede cambiarse con solo pulsar un botón en el software; sin embargo, muchos no entienden el significado de UPR y, por lo tanto, no cambian los ajustes predeterminados.
En ocasiones, ocurre lo contrario. Al no entender que la configuración del filtro afecta de forma considerable a lo que se filtra de los datos o a lo que se conserva para el análisis, los metrólogos pueden verse tentados a elegir una configuración diferente. No obstante, un valor diferente cambiaría los resultados y, por lo tanto, daría lugar a un valor que «parece mejor», pero no es realmente correcto para el tamaño de la pieza de ensayo. En definitiva, lo esencial es que el filtro se configure correctamente para el objeto a medir de que se trate.
Tamaño incorrecto del elemento de palpado
Un segundo error habitual es que los usuarios confíen en un único tamaño del elemento de palpado para medir todas las piezas, sin tener en cuenta el tamaño de la pieza de ensayo con la que están trabajando. De hecho, la esfera de palpado del propio elemento de palpado representa un filtro mecánico que debe seleccionarse en función del tamaño de la pieza de trabajo y del número máximo medible de ondulaciones por revolución.
El ejemplo de un pequeño componente con un diámetro de 4 mm puede servir para ilustrar el problema. Si la superficie de medición se palpa con un palpador dotado de un elemento de palpado demasiado grande, dicho palpador no podrá recorrer correctamente la superficie ni seguir con precisión las subidas y bajadas de los picos y los valles. Del mismo modo, si en un palpador se utilizan elementos de palpado que se aproximan al tamaño en cuestión del diámetro de la pieza de trabajo, resulta muy difícil obtener una buena evaluación de la superficie. En este caso, el uso de este elemento de palpado provoca un filtrado mecánico, incluso antes de que se produzca un filtrado matemático. La hoja 3 de la norma VDI/VDE 2631 ofrece al usuario una guía para seleccionar el elemento de palpado correcto en función de la configuración de ondulaciones por revolución (UPR, por sus siglas en inglés), de la profundidad máxima de onda única esperada y del diámetro de la pieza de ensayo.
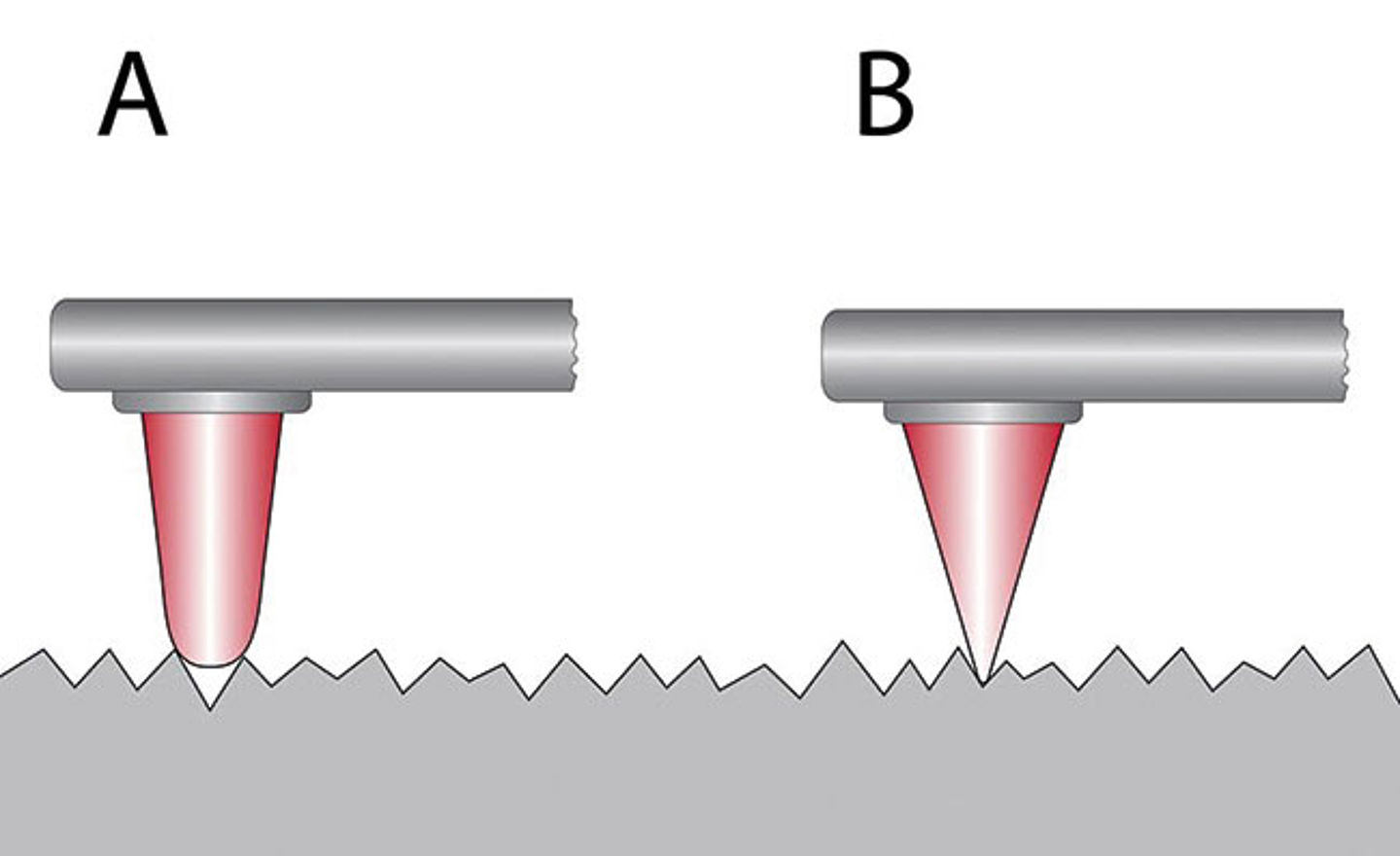
Conclusión
Aunque la medición de formas es una de las tareas básicas en la que se apoyan numerosos procesos de fabricación, muchos usuarios suelen tratar algunos aspectos de forma incorrecta. Esto puede afectar tanto a la fiabilidad de las mediciones como a la calidad global del producto final. Sin embargo, siguiendo algunos pasos básicos, como aplicar correctamente los filtros más adecuados para la situación de que se trate y determinar los datos correctos para cada aplicación, es posible garantizar un resultado preciso. Por otro lado, los accesorios totalmente optimizados, como las esferas de palpado dimensionadas específicamente para la aplicación, permiten que el usuario dé un paso más en lo que se refiere al aumento de la calidad de los datos de medición y, por lo tanto, también de la calidad de la pieza de trabajo.
- Ahorro de tiempo gracias a una alineación eficaz durante la prueba de formas
- MarWin ready: la estación de medición de dentados y formas MarGear GMX 600 W
- Vídeo práctico. Evaluación integral de las piezas de trabajo
- Plataforma de software para la medición económica
- Crear programas de medición sin conexión. Utilizar medidoras de formas de forma económica